With you process map, value stream understanding, and goal of continuous flow, there is one more thing that is critical. How much work is done at each step along the way, how many resources are necessary to insure that work is “pulled” between steps instead of “pushed”. This basically means your staffing and work distribution should be such that when a patient has completed one step, the next step is ready for them, etc. The assembly line should pull rather than each step pushing.
This can be managed by doing a process map of each of the stops in the cycle. The smaller process map will tell you how many tasks, when the time required to complete that step is understood you can consider the staffing required. For example, the triage step requires vital signs, weight, reason for visit, and perhaps other activities in your practice. How much time is required for each activity to achieve the total time? Can each MA manage this step while the prior patient is in with the provider? Or will it be necessary for additional staff since there is more than one provider utilizing the triage station at the same time?
A blog that takes the reader through the principles of Lean Management and Six Sigma in a practical way. The ultimate goal is to help the medical practice to meet its goal of becoming more efficient in providing care and meeting the patients needs. | Contact Owen Dahl at 832-260-4455 or at his website OwenDahlConsulting.com
Thursday, July 31, 2014
Tuesday, July 22, 2014
Continuous Flow

Process Map and Value Stream

Voice of the Customer
The next five posts will highlight the five principles mentioned in the first post.
As mentioned in our introductory post, the VOC is critical to the success of any business but also to the development of and implementation of Lean Management in your medical practice. Just exactly is your customer looking for when they come to your medical practice? They have a list of questions, symptoms or needs. The individual visit is addressed at triage and with the direct encounter with the provider. The patient leaves with a plan and is “happy”!

But why did they choose you in the first place? Did you really meet their expectations during that visit? These are critical questions to find answers. So you now do a patient satisfaction survey and you find out that they don’t like to wait? Can you find out more?
Basics of Lean
Lean Management has been made “famous” by Toyota Motor Company and its “Toyota Production System”, TPS. Authors James Womack and Daniel Jones authored the first major publication, “Lean Thinking” in which they highlighted five principles:
- Value desired by the customer (VOC)
- Value stream for each product/service
- Product (service) flow continuously
- “Pull” between steps
- Manage toward perfection
One of the cornerstones not listed as a principle but certainly key the success of your efforts to become more efficient is to eliminate “muda” or waste! It has long been known, and no one will really argue that we waste time each day. How much time do you and each of your employees waste in a normal day? It is estimated that this will amount to 25% of your day, that’s two hours, that’s 120 minutes! Can you find ways to eliminate 10% of that muda, or 12 minutes? If everyone in the office was more effective for 12 minutes each day, let’s say there are five people in the office that means we have improved productivity by one full hour!
Introduction to This Blog
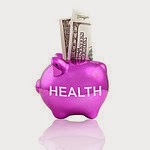
Here is where this blog will come into play. The goal is simple to share ideas and practical solutions with readers on what has been tried and worked or in some cases did not work in achieving the ultimate goal of every medical practice – meet patient expectations by providing the highest quality of care possible.
Peter Drucker said it best when he noted that for a business (the medical practice is a business!) to be successful you must first serve the customer, profits and financial success will follow. The principles behind the management theories of Lean and Six Sigma highlight the “Voice of the Customer”, VOC, as their cornerstone. Focus on meeting the customer needs on everything that is done, every task accomplished in the most efficient way and time, will lead to improved service to the customer.
In this blog, we will look at the principles of Lean Management and Sigma Magma. This may have already turned off some readers! Since these principles started in the manufacturing arena, they cannot nor do they apply to the medical practice. Please read on, I hope to convince you of just the opposite.
Let’s assume the patient has made the phone call and is now at the office prior to their appointment time. They will be checked in, move through triage, visit with the provider, immediate follow up activity as directed by the provider, and check out. This is basically a five-step cycle. If you think it through, each step is sequential and resembles an assembly line!
The first few posts will provide more detail and background on the principles of Lean and Six Sigma. Included will be some practical suggestions on applying those principles. It is hoped that readers will gain benefit from many of these posts and apply the concepts discussed in ways appropriate for their practices. Overtime, it is hoped that readers will share with the author their stories, which will be converted to more practical suggestions for others to attempt.
Remember the ultimate goal is to meet the VOC in a way that is satisfying and at the same time improves their individual health status.
photo credit: via photopin cc
Subscribe to:
Posts (Atom)